Enterprise profile
Established in 1980, Tai Sin Electric Limited is a leading cable and wire manufacturer in Southeast Asia. The company designs, develops, and trades electrical power distribution products for projects across the commercial, residential, industrial and infrastructure sectors. It is listed on the Singapore Exchange mainboard, and is a holding company for 16 other business entities across the region.
Problem statement
Tai Sin’s logistics department had been facing various challenges that affected its efficiency and ability to meet customer demand.
With clients located around the region, it was sometimes difficult to keep track of fluctuating logistics capacities, especially when the company received additional orders that clashed with existing ones.
On a day-to-day basis, pick lists – documents sent to warehouse pickers to fulfil customer orders – would sometimes be issued at the last minute with additional items, leading the logistics department to exceed its capacity. The company would then have to outsource its transportation needs, thus incurring additional costs.
The logistics department also had to manage outdated hardware and software, a challenge that sometimes resulted in longer set-up times for machines used to cut cables. Ad hoc maintenance for the machines also caused delays in the workflow.
All these disruptions affected workforce productivity and order fulfilment times.
“One issue in the production line would lead to another, and it was business critical that we resolve these challenges to boost productivity,” said Mr Cha Poo Chun, Tai Sin’s General Manager.
Impact achieved
Working with Singapore Polytechnic’s Advanced Manufacturing Centre (AMC), Tai Sin was able to upskill its employees and address the pain points that the organisation faced.
AMC trained Tai Sin’s employees to work more efficiently and introduced ways to improve the organisation’s daily planning operations. As a result, they were able to optimise the logistics capacity, cut down on the use of third-party transportation, and save costs.
By streamlining workflows, Tai Sin also increased productivity while minimising disruptions to order fulfilment. At the same time, equipping employees with better product knowledge means they can now set up cutting machines more quickly and address maintenance issues easily, resulting in smoother operations across the company.
In the process, the staff had to overcome challenges such as language barriers and adapting to changes, said Mr Cha. For example, one of the key project members communicates primarily in Mandarin, which hampered communication with his colleagues. Some employees were also not familiar with the concepts used in the training sessions. “But with patient and tailored guidance from AMC, they were able to grasp and embrace the new changes, and effectively implement them,” he noted.
Tai Sin’s management also had to seek the cooperation of other departments, as the issues faced involved more than just the logistics team.
“Communicating these concerns to other departments without sounding accusatory or blaming is crucial to avoid potential pushback and foster a collaborative approach,” said Mr Cha.
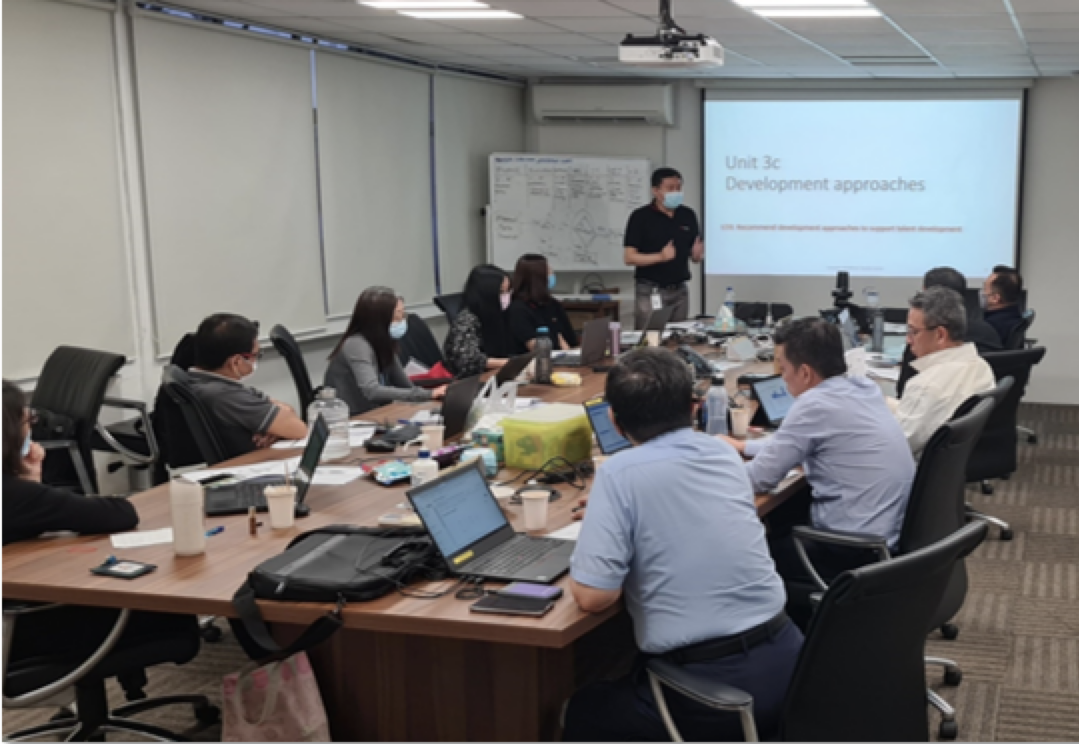
Employees at Tai Sin receiving training from Singapore Polytechnic’s Advanced Manufacturing Centre.